Składniki
Ekran składniki nagranie na YouTube:
- Lista składników pokazuje informację z systemu magazynowego (SM). W Mozarcie również możemy dodawać nowe pozycje. SM i aplikacja to programy zintegrowane, w wyniku tego dodawane pozycje aktualizują się w systemach.
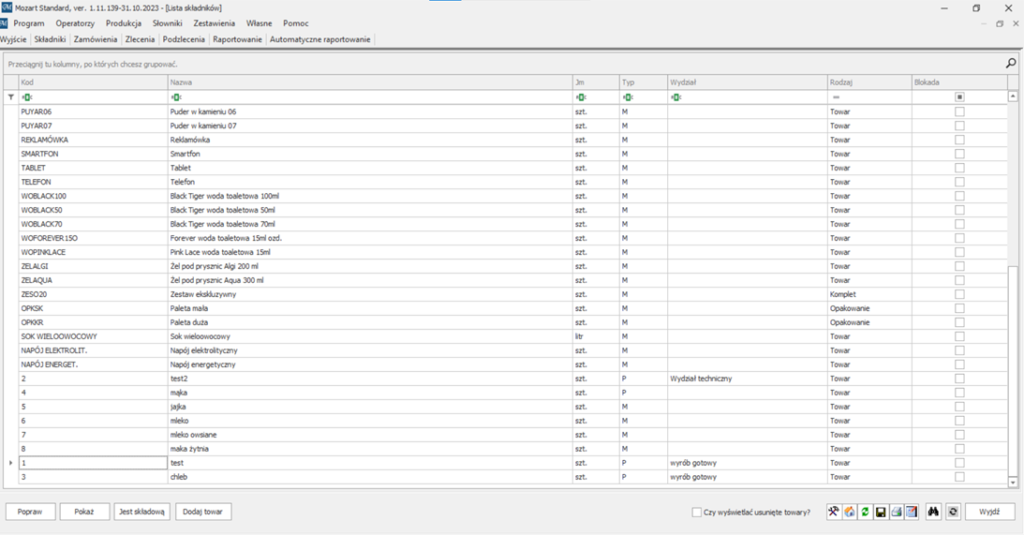
Rys. Lista składników.
- Składniki opisane są następującymi cechami:
- Kod,
- Nazwa,
- jm (jednostka miary),
- Typ (rozróżniamy dwa typy M – materiał i P – produkt),
- Wydział (dotyczy tylko produktów, punkt monitorowania, na którym wykonywany jest produkt),
- Rodzaj (definicje z SM, czy to opakowanie, zestaw, czy towar,
- Blokada (tu możemy ustawić blokadę na wybraną pozycję).
UWAGA: zdarza się, że po wyświetleniu tabeli, widać w niej (kolumna kod) napis „Brak” – oznacza to, że w SM zostały one usunięte z kartoteki (nie należy tego robić w stosunku do składników używanych przez Mozarta tzn. albo będących wg niego pół/produktami lub wchodzącymi w ich skład (pokaże nam to funkcja „Jest składnikiem”) na tym ekranie) Pozycje brak usuną się same jeżeli nie są użyte jako składniki innych produktów. Czyli, jeżeli widzimyje w tabeli “Składniki”, to są gdzieś w strukturach.
- Tabela „Składniki” wyświetla towary i usługi (jeżeli jest tak ustawione w Konfiguracji) z SysMag – w kolumnie „Rodzaj” widać klasyfikację wg SysMag, zaś w kolumnie „Typ” klasyfikację wg Mozarta:
- Typ „M” – „materiał”, coś co nie ma struktury, jest tylko pobierane z magazynu, nie jest produkowane – nie tworzymy na to w Mozarcie pod/zleceń produkcyjnych. Jest to więc coś, co posiadamy w firmie nie w wyniku produkcji, ale (zwykle) zakupu lub usługi własnej. Nie ma zaś znaczenia stopień złożoności: materiałem nazwiemy w Mozarcie zarówno pręt stalowy jak i skomplikowaną szafę sterowniczą, jeżeli tylko ich produkcja odbywa się poza naszą firmą i pozyskaliśmy je w celu produkcji własnych wyrobów przez zakup (lub powierzone).
- Typ „P” – „produkty”, to produkowane (tworzymy na nie w Mozarcie podzlecenia produkcyjne) przez nas pół/produkty, mają strukturę (może być pusta).
Taki element SysMag (może to być tam towar lub usługa) otrzymuje w Mozarcie zestaw dodatkowych parametrów (strukturę, technologie wykonania, informacje kosztowe itp.)
Typ „P” nadajemy w Mozarcie funkcją „Popraw”, poprzez zamianę pozycji typu „M” w „P”.
- Mozart nie rozróżnia właściwie półproduktów od produktów, ponieważ w praktyce okazuje się, że firmy niejednokrotnie sprzedają również półprodukty, bo jakkolwiek np. produkują je właściwie „pod” własną produkcję, to np. w celu maksymalnego obłożenia własnych maszyn dostarczają takie elementy innym lub mają we właściwej ofercie handlowej oba elementy (np. transformatory i zasilacze). Z tej perspektywy nawet istniejący w kartotece znacznik „produkt finalny” ma często znaczenie tylko umowne.
Składniki / przycisk „Popraw”
- Przycisk „Popraw” ma zasadniczo trzy funkcje:
- (jak to napisano powyżej) zamianę materiału (typ „M”) w produkt (typ „P”),
- zamianę produktu w materiał,
- poprawienie danych w istniejącym już produkcie.
„Popraw” / zamiana materiału na produkt (założenie produktu)
Klikając w przycisk Popraw (znajdujący się w lewym, dolnym rogu ekranu listy składników), wywołamy ekran:
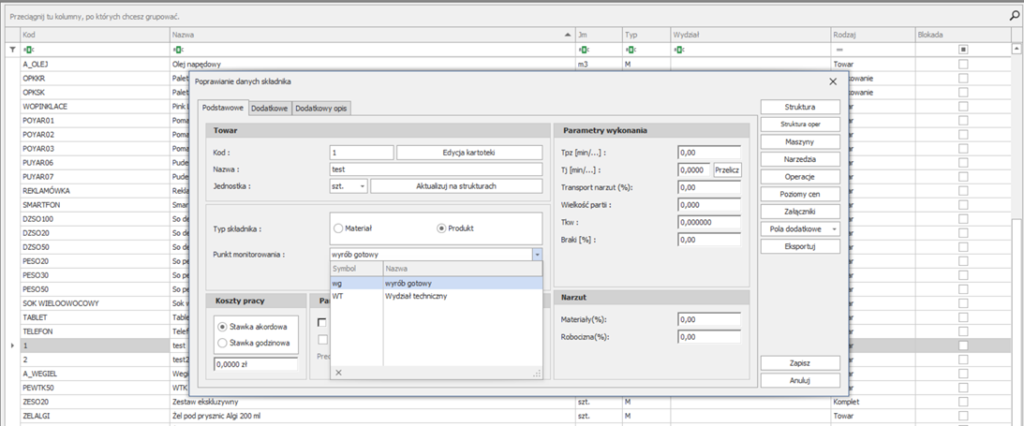
Rys. Poprawianie / zakładanie produktu – zakładka „Podstawowe”,
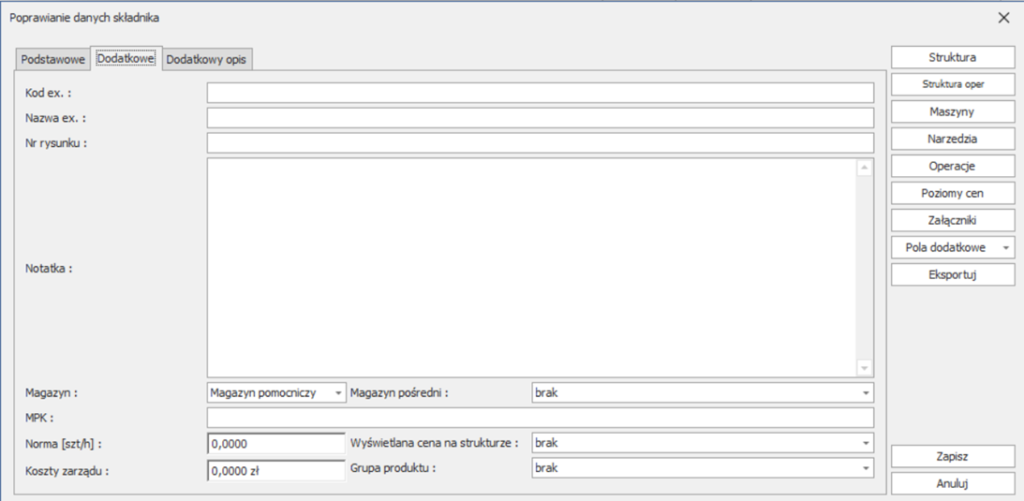
Rys. Poprawianie / zakładanie produktu – zakładka „Dodatkowe”.
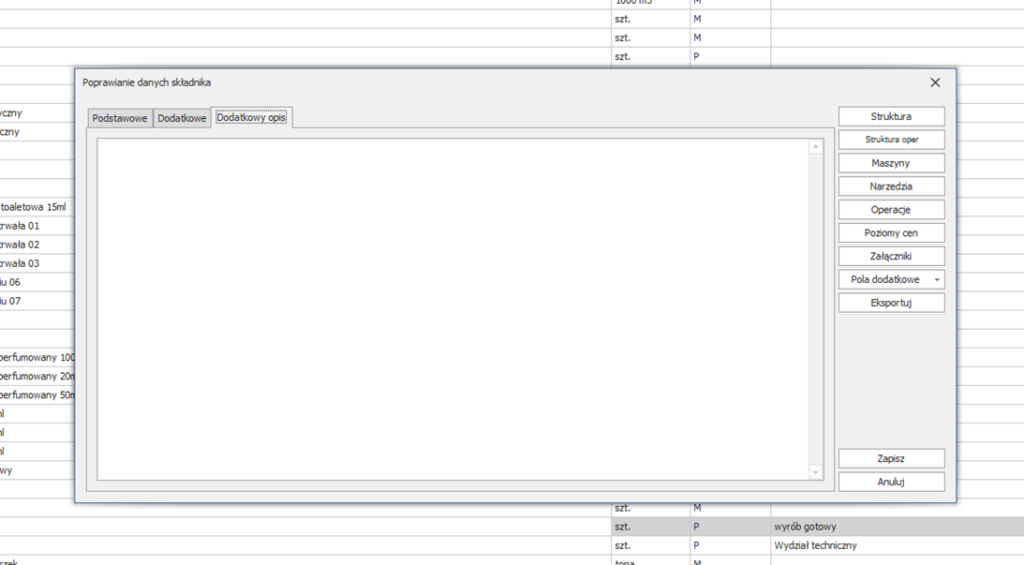
Rys. Poprawianie / zakładanie produktu – zakładka „Dodatkowy opis”.
- Po podświetleniu na liście składników pozycji o typie „M” i naciśnięciu przycisku „Popraw” pojawia się ekran ekran edycji danych składnika – w grupie „Typ składnika” zaznaczamy opcję „Produkt”.
- To powoduje, że – stają się dostępne do edycji inne pola na tej formatce m.in. „Punkt monitorowania”: jest to pole słownikowe, po kliknięciu w które pokazuje się lista PM do wyboru – wybór spowoduje m.in. że podzlecenia na ten półproduktu będą się pokazywały w tej właśnie kolumnie na ekranie zleceń.
- Po wykonaniu dwóch powyższych czynności dokonujemy zapisu – przycisk „Zapisz” – co powoduje powrót do listy składników, lecz obecnie składnik ma typ = „P”. Dzięki temu – po ponownym wybraniu dla niego „Popraw” – będą możliwe do wykonania pewne czynności, inaczej niedostępne np. edycja struktury, która można wykonać tylko dla składników typu „P”.
- Robimy to tzn. ponownie naciskamy „Popraw” dla tego podświetlonego produktu i przechodzimy do właściwej edycji jego danych.
Reszta czynności jest identyczna, jak dla poprawiania dowolnego produktu, bo to właśnie teraz będziemy robić: założyliśmy produkt i poprawiamy jego dane i nie ma znaczenia ile tych danych jest: „nic” jak dla nowo założonego, czy „wszystko” dla dawno założonego i używanego już produktu.
„Popraw” / zamiana produktu w materiał.
- Dokonujemy tego zmieniając w grupie „Typ składnika” opcję „Produkt” na „Materiał”. Należy pamiętać, że aby było to możliwe należy „wyczyścić” ekran struktury produktu tzn. nie może tam być – nawet pustego – wariantu produktu.
”Popraw” / poprawienie danych w istniejącym już produkcie
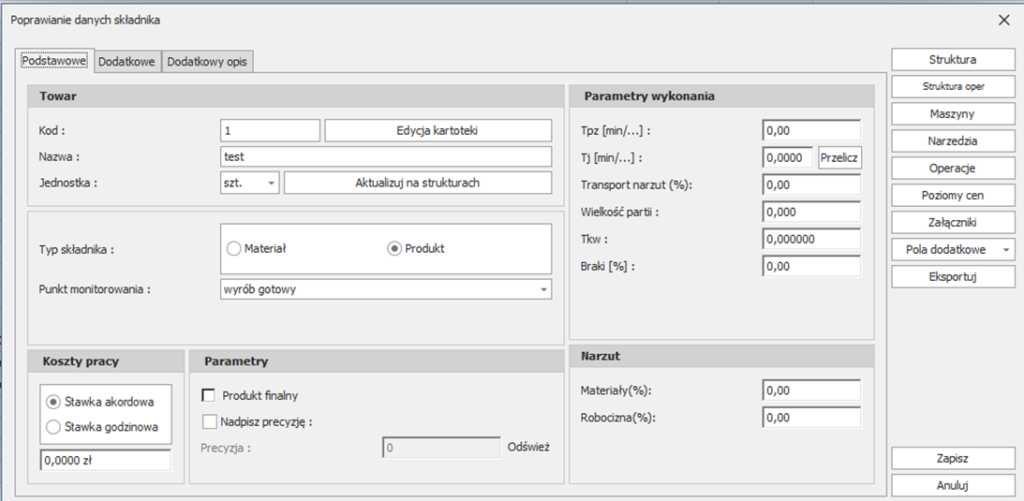
Rys. Edycja danych produktu „Test”
- pole „Kod” (symbol zaimportowany z SM),
- pole „Nazwa” (nazwa j.w.)
- przycisk „Edycja kartoteki” (otwiera kartotekę składnika bezpośrednio w SM – dzięki temu możemy np. wpisać jakieś informacje w pola własne towaru, choćby typoszereg dostępnych opakowań itp.),
- typ składnika:
- Materiał (wartość domyślna, oznaczana na ekranie zleceń literką M, oznaczająca prosty składnik),
- Produkt (oznaczana na ekranie zleceń literką P, jest składnikiem złożonym zbudowanym z innych składników i/lub produktów oraz opisany dodatkowymi parametrami),
- „Punkt monitorowania” (lista, z której wybieramy PM, na którym wykonywane będą podzlecenia dla tego pół/produktu).
grupa „Parametry wykonania”:
- Tpz: czas przygotowawczo-zakończeniowy – ilość czasu potrzebna na przygotowanie maszyny (np. ustawienie parametrów, wymiana głowic itp.) do wykonania serii elementów + czas czynności niezbędnych technologicznie po jej zakończeniu (czyszczenie, demontaż przyrządów itp.),
- Tj: czas jednostkowy – ilość czasu potrzebna na wykonanie jednego pół/produktu
- powyższe oznacza, że łączny czas wykonania np. 10 produktów (cykl produkcyjny) jest równy = Tpz + 10 * Tj,
- „Transport narzut” – opcja obecnie nieaktywna, dodana kiedyś dla utrzymania zgodności z programem „dosowym” firmy Insert („Fabrykant”),
- „Wielkość partii”: tzw. „ekonomicznie uzasadniona minimalna wielkość partii produkcyjnej” oznacza taką ilość produktów, poniżej której nie opłaca się nam produkować np. same koszty przezbrojenia maszyn są wielokrotnie wyższe od możliwych do uzyskania zysków z produkcji. W literaturze tematu jest podanych kilkanaście sposobów – w zależności od uwarunkowań – wyliczenia tej wielkości,
- „Tkw”: techniczny koszt wytworzenia. Alternatywna metoda podania kosztów „pozamateriałowych” – skumulowana, ustalona np. z analizy danych historycznych – wykonania produktu: chodzi o wyliczenie kosztu dokumentu PW, który jest liczony jako koszty użytych materiałów + inne koszty (pracownicy, maszyny, „ogólnozakładowe” itp.).
Jeżeli jest tu podana liczba większa od zera, to ten czynnik jest brany pod uwagę zamiast podanych w grupie „Koszty pracy”.
- „Braki”: podana w procentach wielkość, o którą automatycznie powiększymy wielkość zlecenia (ilość technologiczna na formie zlecenia), aby mimo braków wyprodukować żądaną ilość gotowych produktów. Oczywiście wpływa to również zapotrzebowanie materiałowe, ewentualne zamówienia do dostawców itd.
Jeżeli więc np. klient zamówił 100 egzemplarzy, a my z badań statystycznych wiemy, że ilość braków przy produkcji tego produktu jest 5% i wpiszemy w pole „Braki” liczbę 5, to Mozart powiększy ilość do produkcji do 105. aby nawet w pesymistycznym przypadku zamówienie klienta zostało zrealizowane.
UWAGA: jeżeli dotyczy to (braki) produktów tanich lub często kupowanych, to nie ma problemu. Jednak w przypadku produktów drogich i/lub unikalnych należy się zastanowić, czy ten mechanizm stosować, a wręcz być może nie wpisywać w kartotekę produktu szacowanej ilości „Braków”, jest to bowiem ilość szacunkowa i nie musi wystąpić, a wtedy zbędnie wyprodukowane produkty, a nawet nadmiarowo – w wyniku takiego planowania – zamówione surowce, mogą być poważnym problemem.
grupa „Koszty pracy”:
- Stawka akordowa: to stawka wypłacana pracownikowi za wykonanie jednego produktu. Może być też użyta „dla celów technicznych” jako koszt produkcji „pozamateriałowy” przypadający na jeden produkt i wykorzystany np. przy liczeniu kosztu dokumentu PW.
- Stawka godzinowa: to stawka przysługująca pracownikowi za każdą godzinę poświęconą przy wykonywaniu danego produktu. Może być też użyta „dla celów technicznych” jako koszt produkcji „pozamateriałowy” przypadający na każdą godzinę związaną z produkcją danego produktu i wykorzystany np. przy liczeniu kosztu dokumentu PW.
grupa „Parametry składnika”:
- Precyzja: dla każdego towaru ustawiana jest precyzja oznaczająca ilość miejsc po przecinku, jaka jest brana przy podawaniu/ustalaniu ilości produktu, wyznacza poziom zaokrąglania.
Przykład:
(zakładamy, że w Konfiguracji / Magazyny jest zaznaczona opcja „Uwzględniaj precyzję”, bo inaczej wpisy w kartotece produktu są nieaktywne)
- wpisaliśmy 5% w pole „Braki”
- wpisujemy, przy zakładaniu zlecenia w pole ilość (IL) =10 – wtedy bez uwzględniania precyzji w ilości technologicznej (IT) pojawi się 10,5 co może nie mieć sensu dla produkcji stołów o jednostce magazynowej „sztuki” (gdyby były „tysiące” problem by nie istniał). Co zrobić?
- precyzja oznacza, na którym miejscu po przecinku chcemy mieć (po uwzględnieniu % braków) „sensowną” (z punktu widzenia stosowanej jednostki miary) ilość: ponieważ nie akceptujemy dla stołów ułamkowych ilości, więc wpisujemy w „Precyzja” = 0 i skutkiem tego, przy zakładaniu zleceni, w ilości technologicznej pojawia się 11. Poniżej różne kombinacje:
- braki= 5% PRC= 0 IL= 10,0 IT= 11,0
- braki= 5% PRC= 1 IL= 10,0 IT= 10,5
- braki= 12,5% PRC= 0 IL= 10,0 IT= 12,0
- braki= 12,5% PRC= 1 IL= 10,0 IT= 11,3
- braki= 12,5% PRC= 2 IL= 10,0 IT= 11,25
Uwaga: jeżeli zlecenie zostało założone poprzez kopiowanie innego, to przepisuje jego wpisy, a jeżeli w międzyczasie precyzja się zmieniła, to przeliczenie trzeba wymusić poprzez wpisanie w „ilość technologiczną” liczby mniejszej niż w polu „ilość” i kliknięcie w pole ilość.
Precyzja jest brana pod uwagę przy:
- Bilansowaniu – wyliczanie na podstawie ilości planowanej ilości do produkcji – doliczany jest procent braków z określoną precyzją.
- Przy tworzeniu zlecenia z zamówienia – wyliczanie na podstawie ilości planowanej ilości do produkcji – doliczany jest procent braków z określoną precyzją.
- W zleceniu głównym – po wpisaniu ilości planowanej liczona jest ilość do produkcji.
- W trakcie raportowania zlecenia – przy generowaniu odpadów z produkcji – ilość odpadu jest zaokrąglana do precyzji – odpowiedniej dla każdego odpadu.
- W trakcie dodawania składnika do struktury produktu, jeżeli w konfiguracji jest to ustawione, to jest kontrolowana precyzja z jaką wprowadza operator dany składnik (zgodnie z def. Składnika).
- Może to mieć tez wpływ na wystawianie dokumentów np. brak PW na odpad będzie występował wtedy, gdy precyzja była dla produktu ustawiona na “zero”, a wyliczona wg receptury ilość odpadu jest poniżej “jednej” jednostki (np.0,4kg) – należy wtedy zmienić odpowiednio precyzje na np. 1.
- Produkt finalny: praktycznie, zaznaczenie tej opcji oznacza, że dokument PW na produkt będzie generowany w „magazynie produktów” (wg Konfiguracji zakładka Magazyny). Dlatego stosowane jest to głównie dla produktów końcowych (przeznaczonych do sprzedaży).
grupa „Narzut”:
W kartotece produktu są dwa pola (narzuty procentowe):
- Narzut materiały
- Narzut praca
- przy generowaniu zleceń pola są przenoszone do zlecenia
- przy liczeniu kosztów doliczane są w dokumencie PW wprowadzone narzuty procentowe wg wzoru:
Koszt PW = (Koszt RW + (a)% ) + (“Obecne” koszty pracy + (b)% )